Developing a Welding WPS: Step-by-Step Directions for Professionals
Opening the Power of Welding WPS: Methods for Efficiency and Security in Fabrication
In the realm of fabrication, Welding Procedure Specs (WPS) stand as the backbone of welding procedures, determining the necessary actions for accomplishing both effectiveness and safety in the fabrication process. Understanding the complexities of WPS is critical to using its full possibility, yet numerous organizations struggle to open real power that exists within these records (welding WPS). By diving right into the techniques that maximize welding WPS, a world of enhanced productivity and enhanced safety and security waits for those ready to explore the subtleties of this vital element of manufacture

Significance of Welding WPS
The value of Welding Treatment Specifications (WPS) in the manufacture industry can not be overstated. WPS serve as a crucial roadmap that lays out the essential steps to make certain welds are performed consistently and appropriately. By specifying necessary specifications such as welding processes, products, joint layouts, preheat temperatures, interpass temperatures, filler steels, and post-weld warmth therapy requirements, WPS provide a standard technique to welding that enhances performance, quality, and security in construction procedures.
Adherence to WPS assists in accomplishing uniformity in weld quality, decreasing the probability of defects or structural failures. This standardization likewise assists in conformity with industry guidelines and codes, guaranteeing that fabricated structures fulfill the called for safety and security criteria. Furthermore, WPS paperwork enables welders to reproduce effective welding treatments, bring about regular outcomes across different jobs.
In essence, the precise development and strict adherence to Welding Treatment Requirements are extremely important for promoting the honesty of bonded structures, protecting against possible threats, and supporting the credibility of fabrication companies for supplying high-grade product or services.
Key Aspects of Welding WPS
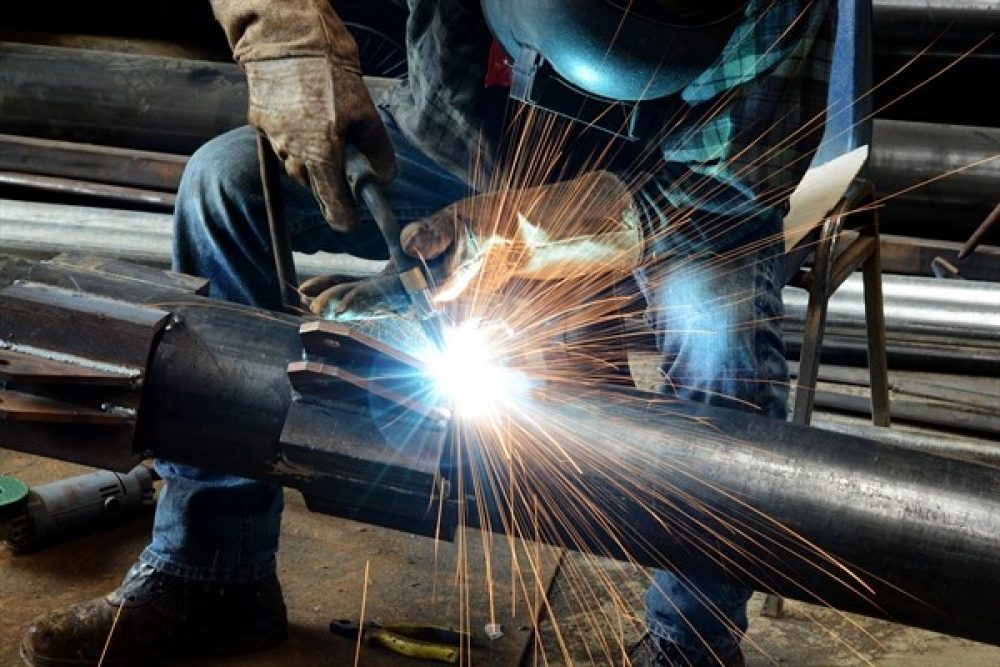
Enhancing Effectiveness With WPS
When optimizing welding procedures, leveraging the crucial elements detailed in Welding Procedure Requirements (WPS) becomes essential for enhancing processes and maximizing efficiency. One means to enhance effectiveness with WPS is by meticulously picking the suitable welding specifications. By adhering to the certain guidelines given in the WPS, welders can guarantee that the welding tools is set up appropriately, leading to top quality and constant welds. Additionally, complying with the pre-approved welding series outlined in the WPS can dramatically minimize the moment invested in each weld, ultimately increasing general performance.
Frequently click to read reviewing and updating the WPS to incorporate any type of lessons learned or technological innovations can likewise contribute to performance improvements in welding operations. By welcoming the guidelines established forth in the WPS and continually seeking methods to optimize procedures, fabricators can achieve higher effectiveness levels and superior end outcomes.
Ensuring Security in Fabrication
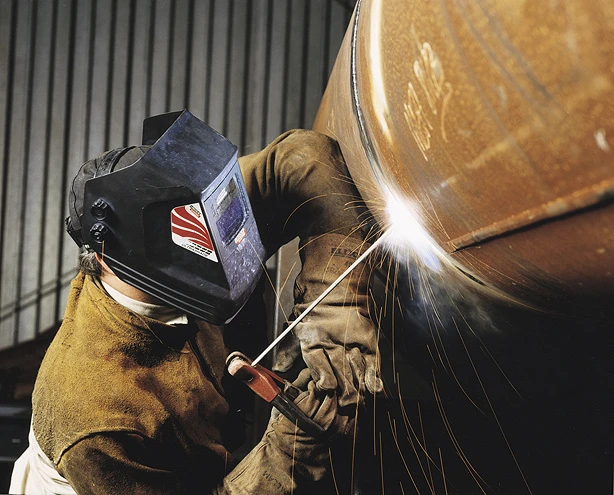
Making sure security in construction involves a multifaceted strategy that incorporates different aspects of the welding process. Welders must be outfitted with ideal gear such as helmets, handwear covers, and safety clothing to mitigate dangers associated with welding tasks.
In addition, adherence to proper ventilation and fume extraction systems is crucial in maintaining a healthy job atmosphere. Welding fumes include harmful materials that, if inhaled, can position significant health dangers. Applying reliable ventilation steps aids to minimize direct exposure to these dangerous fumes, advertising breathing health amongst workers.
Normal equipment upkeep and examinations are additionally vital for ensuring safety and security in fabrication. Damaged machinery can cause injuries and crashes, underscoring the importance of prompt repair work and regular checks. By focusing on security actions and fostering a society of recognition, fabrication facilities can produce a productive and protected workplace for their employees.
Implementing WPS Ideal Practices
To improve functional effectiveness and ensure top quality results in manufacture procedures, integrating Welding Procedure Requirements (WPS) best practices is extremely important. Choosing the appropriate welding process, filler product, and preheat temperature defined in the WPS is important for accomplishing the wanted weld high quality. Ensuring that qualified welders with the essential accreditations bring out the welding procedures according to the WPS standards is essential for uniformity and dependability.
Verdict
Finally, welding WPS plays a critical role in resource making sure efficiency and security in manufacture processes. By concentrating on vital components, enhancing effectiveness, and implementing best methods, firms can optimize their welding procedures. It is important to focus on precaution to protect against accidents and make certain a smooth manufacturing process. By adhering to these methods, organizations can open the complete capacity of welding WPS in their construction procedures.
In the world of fabrication, Welding Procedure Specifications (WPS) stand as the foundation of welding operations, dictating the essential steps for achieving look at this site both performance and security in the fabrication process. By defining necessary criteria such as welding procedures, products, joint layouts, preheat temperature levels, interpass temperature levels, filler steels, and post-weld warmth therapy demands, WPS supply a standard technique to welding that improves effectiveness, high quality, and security in manufacture procedures.
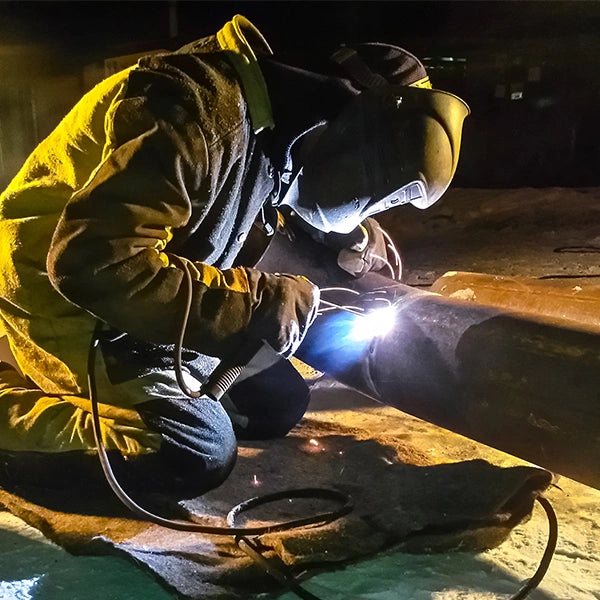
When maximizing welding operations, leveraging the crucial components outlined in Welding Procedure Requirements (WPS) becomes necessary for optimizing and streamlining procedures performance. (welding WPS)